Experience – tailored to your product
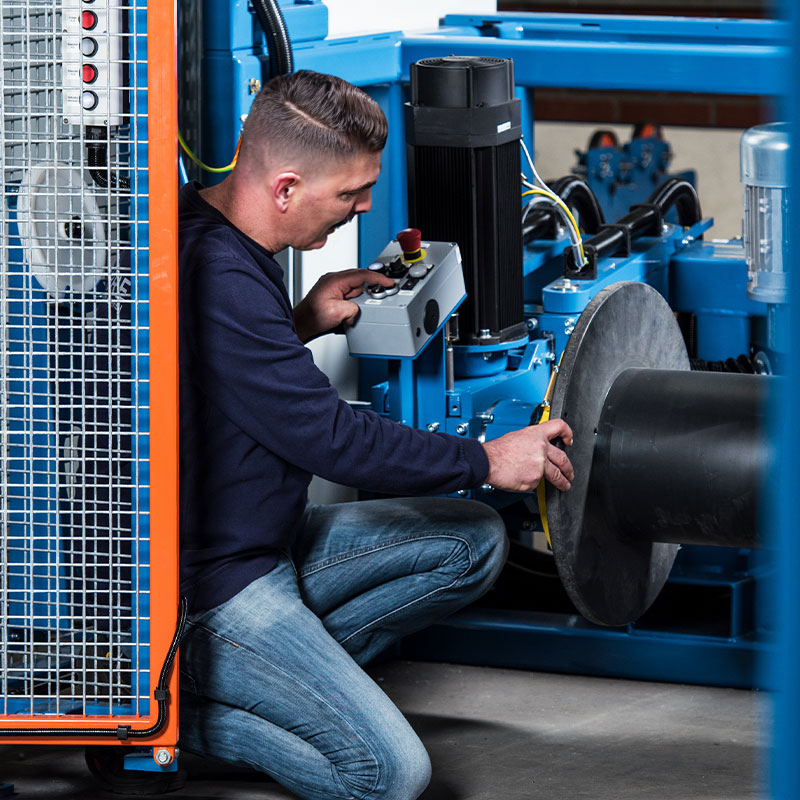
Your request – our solution
CUSTOMIZED INDIVIDUALITY
Our strength lies in our individuality. Almost every machine is specially adapted, designed and built in our company for the respective customer. In the design department we have more than 30 engineers who are responsible for the mechanical and electrical design of the machines.
We excel in solving problems. We are also happy to develop completely new machines together with you, which we will construct as unique models. Customized solutions, off the standard, are our daily tasks.
Above all, we work with guaranteed quality standards. Hence, you are guaranteed the highest quality possible, durabilty and reliability.
Research + Development
SIEBE ENGINEERING INSIDE

Since 2017 the expert for complex extrusion systems has been part of KURRE Systems and completes our portfolio. “SIEBE inside” stands for decades of quality in the field of plasticizing various polymers and extrusion technology. Ongoing laboratory trials and test series are constantly refining this technology – for high-quality products and reliable systems.
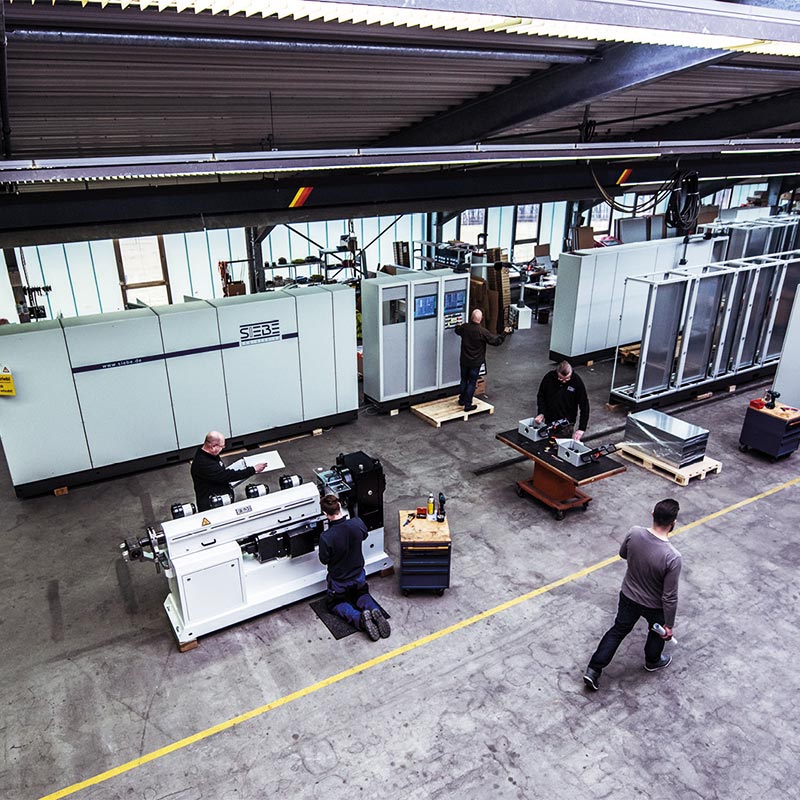
Challenge us
OUR COMPETENCIES
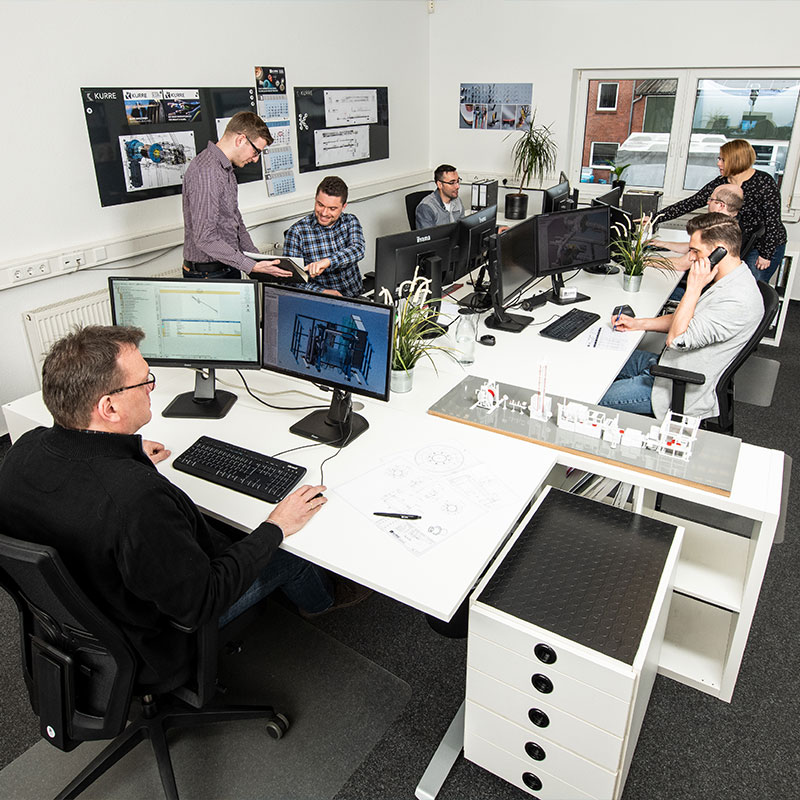
Design
3D DEVELOPMENT, MECHANICAL DESIGN AND SIMULATION
Machines made by KURRE are adapted to special customer requirements. The implementation is done in the SolidWorks design system and in close cooperation between design, project management and you. For communication and release, you will receive 3D-PDFs with all relevant details.

Electrical design
CONSISTENT, CONTINUOUS AND QUICK
The electrical design for our machines and lines is carried out exclusively in the E-Plan P8 engineering system and is therefore consistent, continuous and quick. Once documented in the circuit diagram, the project data forms the basis for our internal production of all electrical components such as terminal boxes, control cabinets or operating elements.
The use of the most modern bus systems, remote diagnosis options and user interfaces ensures a state-of-the-art system.
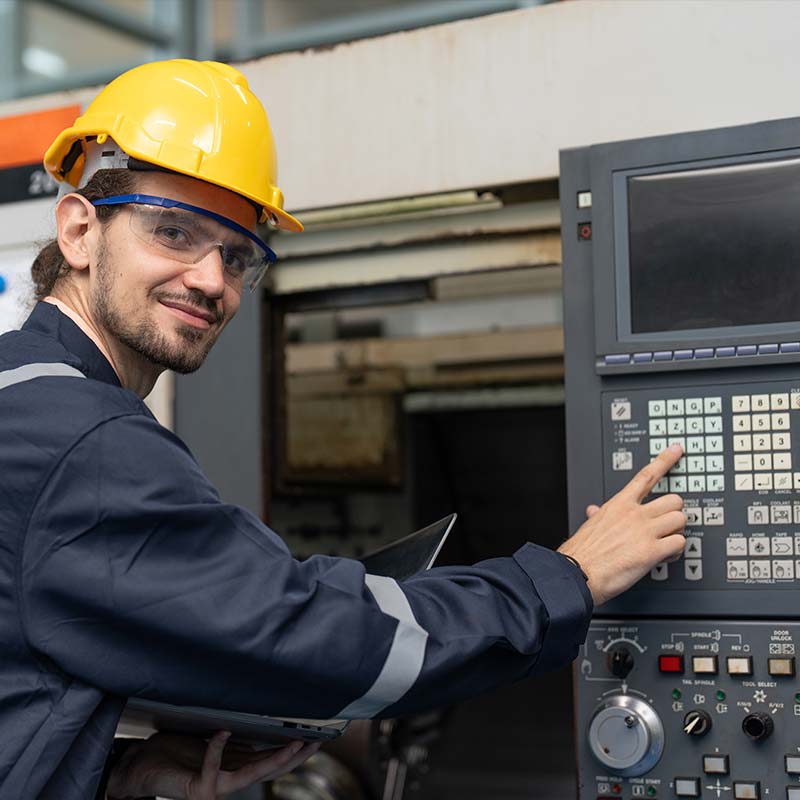
COMMISSIONING
BRING TO LIFE
All machines are completely assembled in our company and are put into operation and tested with all their functions. This is in fact the perfect quality assurance, because these tests combine tests of geometric manufacturing tolerances, electrical wiring and theoretically programmed functions.
These extensive tests are carried out with original customer material. In order to prove all functions according to the specifications, these tests are carried out at Kurre. Afterwards, the customer approves the transport and the subsequent shipment.
This procedure ensures a fast and effective integration into the customer’s production environment.
The KURRE promise
YOUR ADVANTAGE
KURRE Systems can look back on a long tradition in mechanical engineering – especially in the cable industry. Knowledge of our customers’ processes makes all the difference. Because only those who understand the manufacturing process of a product can offer the perfect solution.
As our customers and their requirements for high-quality products are always our focus, our systems and machines are as individual as the products our customers use them to manufacture. In addition to customized system solutions, our unique vertical manufacturing range of more than 90% is what sets us apart. This gives us and our customers exceptional flexibility.
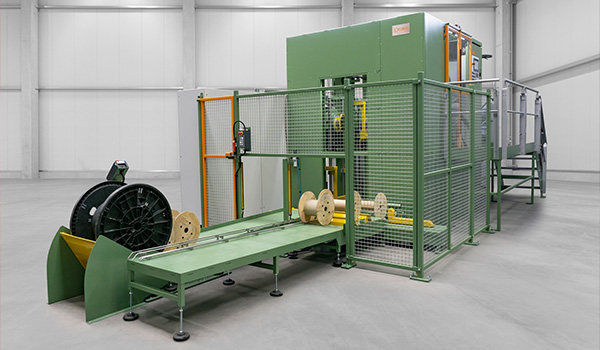
Our employees are the basis for implementing complex tasks. We have all processes for the realization of machine and system projects in-house, i.e. we map the entire development process. We continuously invest in our work and production equipment at two locations in Germany. The result is machines and systems that are characterized by high-quality materials, reliability and durability. We have been working with many of these machines and systems for several decades. This means that our products are not just “Made in Germany”, but “Made by KURRE”.
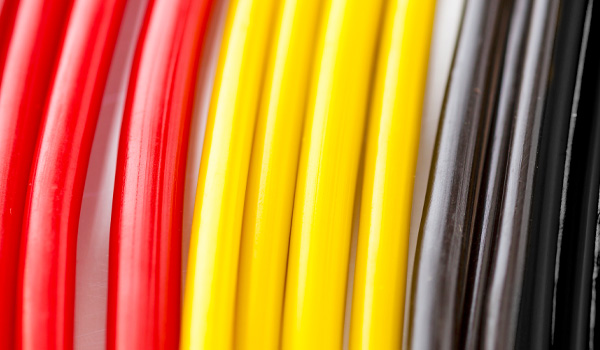
Our consistent in-house production not only strengthens the quality of our solutions, but also underlines our commitment to the security and exclusivity of our contractual partners’ information. At the same time, this capability puts us in a position to manufacture spare parts within a very short space of time, enabling us to offer customers optimum service in the event of an emergency.
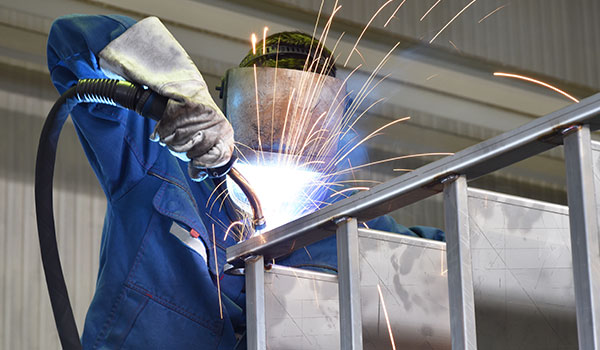
Based on the decades of experience of our employees, we already address the specific requirements of our customers during the sales process. Detailed quotations form the basis for the exact implementation of customer requirements within our design department. Whether it is the mechanical realization of the systems or the perfect electrical equipment – we always keep an eye on the technical functionality of our products. In close cooperation with our customers, we create customized solutions.

A quick introduction
OUR SKILLS AND EXPERTISE
This machine type is used in the production of plastic granulate. Strands are extruded from powdered raw materials or recycled plastic, which are then crushed in a further production step. The resulting granulate is then the raw material for other plastics processing machines.
KURRE supplies customized extruders for this application and, if required, also adapts them to the respective granulating line.
In contrast to conventional extrusion processes, hot melt extrusion is characterized by an intermittent mode of operation.
High-dynamic drives are required to compensate for the strong pressure fluctuations when opening or closing the application valve.
This system component was designed and built by our project team to separate sheathed fluorescent tubes from the extruded strand in a continuous process. This is another example that demonstrates our ability to develop, implement and operationalize custom solutions.
In automotive production, plastic components are used in many areas of the car body. These plastic parts are painted in all available vehicle colors. This is done using highly automated coating lines in which the parts must be specifically picked up and positioned. Using Solid Works 3D data, we design and manufacture these coating racks.
The correct positioning of the plastic parts guarantees an optimal finishing. We also manufacture ergonomically designed assembly racks for subsequent processing and equipping with components. These include, for example, headlight cleaning systems, distance sensors or similar.
Shower trays are molded from certain concrete materials. The material is viscous and must be processed under a respiratory protective mask within a specified period of time. The material properties fluctuate with the natural environmental conditions depending on the seasons.
The wide variety of shower tray geometries places further high demands on automation. Programmes must be flexibly configirable allowing the user the ability to create independent programme variations at any time. This function was also designed, built and programmed by our project team.